Advanced technology in plastic extrusion for current industries
Advanced technology in plastic extrusion for current industries
Blog Article
A Comprehensive Guide to the Refine and Benefits of Plastic Extrusion
In the vast world of production, plastic extrusion emerges as a extremely effective and essential process. Translating raw plastic right into continual profiles, it provides to a variety of markets with its remarkable adaptability.
Understanding the Basics of Plastic Extrusion
While it may appear facility initially glance, the process of plastic extrusion is basically simple - plastic extrusion. It is a high-volume manufacturing method in which raw plastic is melted and shaped into a continual profile. The process starts with the feeding of plastic product, in the form of pellets, powders, or granules, into a warmed barrel. The plastic is then thawed using a combination of heat and shear, applied by a turning screw. As soon as the molten plastic gets to completion of the barrel, it is required through a little opening understood as a die, forming it into a wanted kind. The shaped plastic is then cooled, strengthened, and reduced into wanted sizes, completing the process.
The Technical Process of Plastic Extrusion Explained
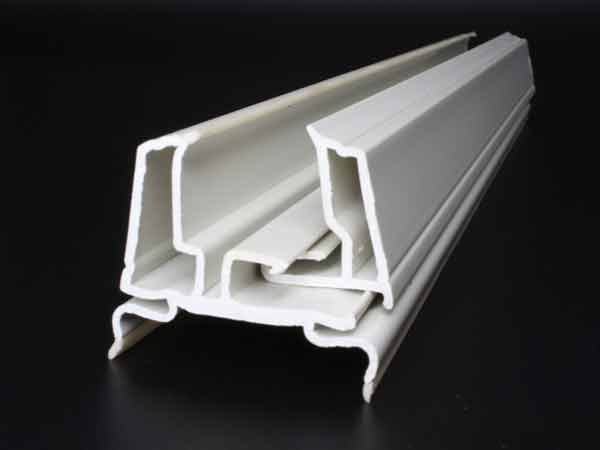
Kinds Of Plastic Suitable for Extrusion
The selection of the ideal type of plastic is a critical facet of the extrusion process. Various plastics offer special residential properties, making them a lot more matched to certain applications. Polyethylene, for example, is generally used due to its inexpensive and easy formability. It uses excellent resistance to chemicals and dampness, making it optimal for products like tubing and containers. Similarly, polypropylene is another prominent selection due to its high melting factor and resistance to fatigue. For more durable applications, polystyrene and PVC (polyvinyl chloride) are commonly selected for their stamina and sturdiness. These are typical alternatives, the option ultimately depends on the specific requirements of the product being produced. So, understanding these plastic types can significantly improve the extrusion procedure.
Contrasting Plastic Extrusion to Other Plastic Forming Approaches
Comprehending the sorts of plastic suitable for extrusion leads the way for a wider discussion on how plastic extrusion compares to various other plastic forming techniques. These consist of shot molding, strike molding, and thermoforming. Each method has its one-of-a-kind usages and benefits. Shot molding, for circumstances, is excellent for producing complex components, while impact molding is perfect for hollow objects like containers. Thermoforming excels at creating shallow or big components. However, plastic extrusion is exceptional when it comes to producing constant accounts, such as pipelines, seals, and gaskets. It additionally enables a consistent cross-section along the size of the product. Hence, the option of method mainly relies on the end-product requirements and specifications.
Trick Benefits of Plastic Extrusion in Production
In the world of production, plastic extrusion offers numerous substantial benefits. One remarkable benefit is the cost-effectiveness of the procedure, that makes it an economically attractive production method. In addition, this technique provides remarkable item versatility and improved manufacturing speed, therefore enhancing overall manufacturing effectiveness.
Affordable Manufacturing Approach
Plastic extrusion leaps to the forefront as a cost-effective production approach in manufacturing. Furthermore, plastic extrusion requires less power than typical production techniques, adding to lower functional expenses. In general, the monetary advantages make plastic extrusion a highly attractive choice in the production industry.

Superior Item Adaptability
Past the cost-effectiveness of plastic extrusion, an additional substantial benefit in producing hinge on its premium item adaptability. This process enables for click for more the creation of a vast array of products with differing sizes, forms, and layouts, from basic plastic sheets to detailed accounts. The adaptability is credited to the extrusion die, which can be personalized to generate the preferred product design. This makes plastic extrusion an ideal remedy for markets that require tailored plastic components, such as vehicle, building and construction, and packaging. The capacity to generate varied items is not only valuable in conference specific market demands however also in making it possible for suppliers to check out new product with minimal capital financial investment. Fundamentally, plastic extrusion's product versatility promotes development while boosting operational performance.
Enhanced Production Speed
A substantial advantage of plastic extrusion depends on its boosted manufacturing rate. This manufacturing process allows for high-volume manufacturing in a reasonably brief time span. It is capable of producing long, constant plastic profiles, which significantly lowers the manufacturing time. This high-speed manufacturing is specifically helpful in markets where large quantities of plastic parts are required within tight due dates. Few various other production procedures can match the speed of plastic extrusion. Furthermore, the capability to keep regular high-speed manufacturing without giving up item high quality establishes plastic extrusion apart from other methods. The enhanced manufacturing speed, for that reason, not just enables manufacturers to meet high-demand orders however also adds to enhanced performance and cost-effectiveness. This beneficial attribute of plastic extrusion has actually made it a favored selection in many sectors.
Real-world Applications and Impacts of Plastic Extrusion
In the world of manufacturing, the strategy of plastic extrusion holds extensive significance. This procedure is commonly made use of in the manufacturing of a selection of items, such as plastic tubing, home window structures, and weather stripping. Therefore, it significantly affects sectors like building, product packaging, and vehicle industries. Its impact prolongs to daily things, from plastic bags to tooth next brushes and non reusable flatware. The economic advantage of plastic extrusion, mainly its high-volume and cost-effective outcome, has transformed manufacturing. Nonetheless, the ecological impact of plastic waste continues to be a worry. The market is persistently striving for technologies in naturally degradable and recyclable products, indicating a future where the benefits of plastic extrusion can be preserved without compromising ecological sustainability.
Conclusion
In verdict, plastic extrusion is a reliable and very reliable technique of transforming basic materials into varied products. It uses numerous advantages over various other plastic creating methods, including cost-effectiveness, high output, marginal waste, and layout adaptability. Its effect is profoundly felt in different industries such as building, vehicle, and durable goods, making it a pivotal process in today's manufacturing landscape.
Delving deeper right into the technical procedure of plastic extrusion, it starts with the selection of the suitable plastic material. Once cooled down, the plastic is reduced into the called for lengths or injury onto reels if the product is a plastic movie or sheet - plastic explanation extrusion. Contrasting Plastic Extrusion to Other Plastic Forming Techniques
Understanding the kinds of plastic appropriate for extrusion leads the way for a more comprehensive conversation on exactly how plastic extrusion stacks up against other plastic developing approaches. Couple of various other manufacturing procedures can match the speed of plastic extrusion.
Report this page